In choosing to do this experiment, I will look only at how the lubes affect lock speeds. Others have examined a lubes resistance to rust formation. Many lubes have been suggested. I will try to choose those that are widely used or represent a group of lubricants.
The text here is in progress. It’s kind of like diary entries showing all the problems associated with a test of this kind. I’ll straighten it up later.
I brought my testing set-up into the basement . My garage is heated but I’d rather not run temps up and down because of some old cars. Will if I have to. I will be testing infrared gates and beginning to figure out the methods.
I have to thank an ALR guy for a real stroke of luck. He offered me a sample of colonial period oil to include in the tests. That gives us a chance to include what I expect is the best of colonial lubes available.
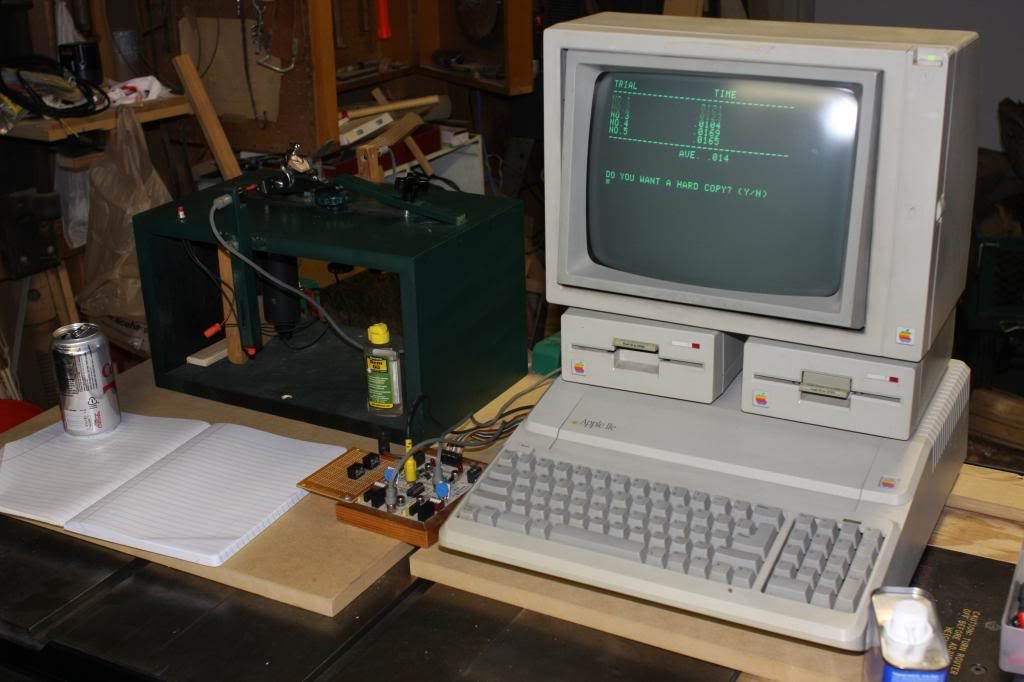
Progress has been slow today. I spent my time solving problems with infrared gates. They have always been troublesome, but today static electricity in my dry basement and the sensitivity adjustments have taken too much time. A potentiometer may need to be replaced. There are a few fixes to try before I resort to that though. During teh afternoon I did get a dry run done using Rem oil on the lock. Numbers ran from .0160 to .0220 seconds. This won’t be used as a bench mark because the sensitivity may change the results. So, nothing final here, just some slow progress.
I finally solved the gate sensitivity today. I replaced the two potentiometers on the interface board. These seem to adjust smoothly and give me much more control of the gate sensitivity. I did a short test and feel I’m ready to begin the testing.
The cleaning method is my next problem. My plan is to do a three stage cleaning. First the lock goes into warm water with a little dish soap added and be scrubbed. Next into rinse water and blown dry. Lastly I’ll use acetone or alcohol to do a final rinse and blow dry. That should leave the lock absolutely lube free.
Beginning each set of trials and after applying lube, I’ll snap the lock a couple of times before timing the first trial. Hope things go well.
Today I tested six lubes against a trial with no lube at all. My gut said that the lubed tests would be pretty close with the no lube slower. This was not the case, however. The no lube trial averaged in the middle of the lubed scores. Below are the lubes in the order they finished with their average for 10 trials:
A few comments need to be made about these scores and lubes. First it was very hard to clean the lube off between trials. I had to wash the lock carefully in alcohol. This last step had to be done more than once in some cases. I timed the no lube first and realized I didn’t wash it thoroughly enough, and had to toss the times. If I used those numbers, no lube would have been in first place. Cleaning definitely is the crucial step here.
The trials are in the order of testing left to right. The “no lube” in the left column is the one in which I felt I did not clean well enough to use. Instead I decided to retest at the end. That trial is on the far right. The times within each trial are in order from top to bottom. This is probably not as significant as it would be if a flint edge was used. The range within each trial was wider than I expected. The exception is in the Ballistol group where the range is significantly smaller than the rest. It was the slowest in the group also.
The infrared gates worked better than before I swapped the parts on the board. I got a few scores out of range, but not many.
The Chambers product was a 2 part lube. A white grease was used between main spring and tumbler and also on the frizzen spring. A thin oil was used on the rotating parts. The white grease was very hard to clean off after this test.
The “Colonial” oil sample was the only sample that would be historically correct.
The individual times in each set were more widely spread than I was expecting. The averages were in the ball park with earlier timing. The mechanical times for this same lock, published in the JHAT vol IV, was .0151 seconds IIRC. .
I have a number of other lubes to try, however my cold wore me out and I stopped with these today. I will probably try to get a few more done, but after today I think I know how it will turn out. (I didn’t do my favorite which is Rem Oil.) I’ll continue to look at the numbers for any trends.
I want to continue to mull all this over, but I think the differences are statistically insignificant. The ranges of trials were too wide to be decisive. In fact the narrowest range was for Ballistol, the slowest average. This would be easier to see if you could see the group of scores for each lube. I’ll try to see to that.
I do like Jim’s lube combination. The lube for sliding surfaces makes sense. Between shooting sessions, I would use a lube based on its rust prevention. I better let it go for now. This needs more thought.
Here are a few photos of the setup and the spreadsheet that includes all the trials:
This is the overall setup I’m using.
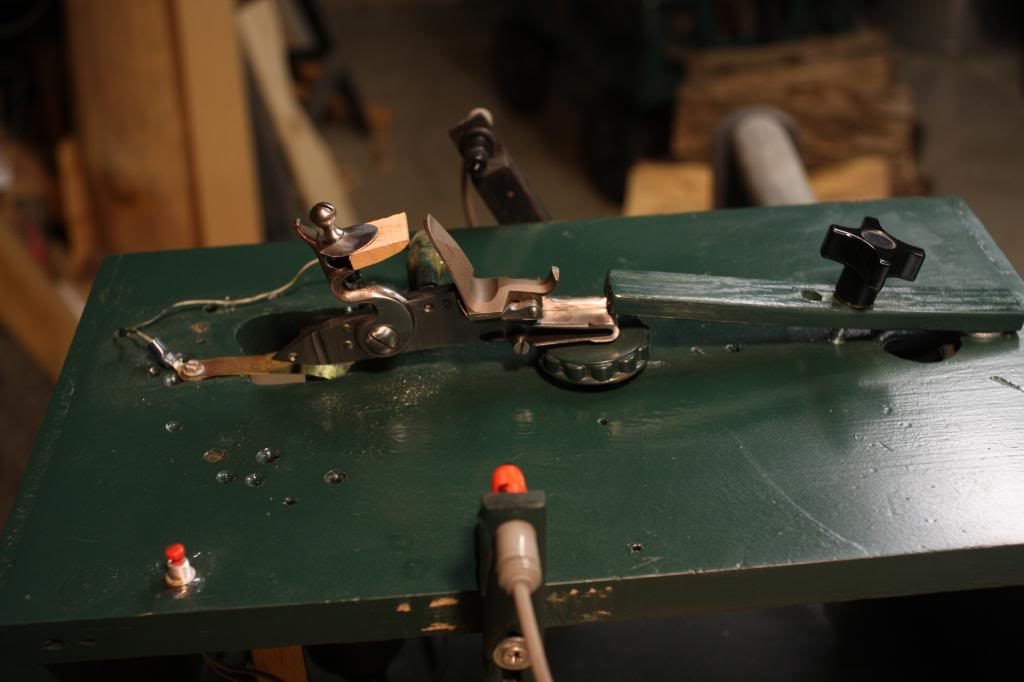
This pic shows the fixture with the Siler installed. The orange RCA plug in the forground holds the led emiter, while in the background is the detector (black). The infrared beam is positioned right above the frizzen. When the frizzen rises, the beam is broken.
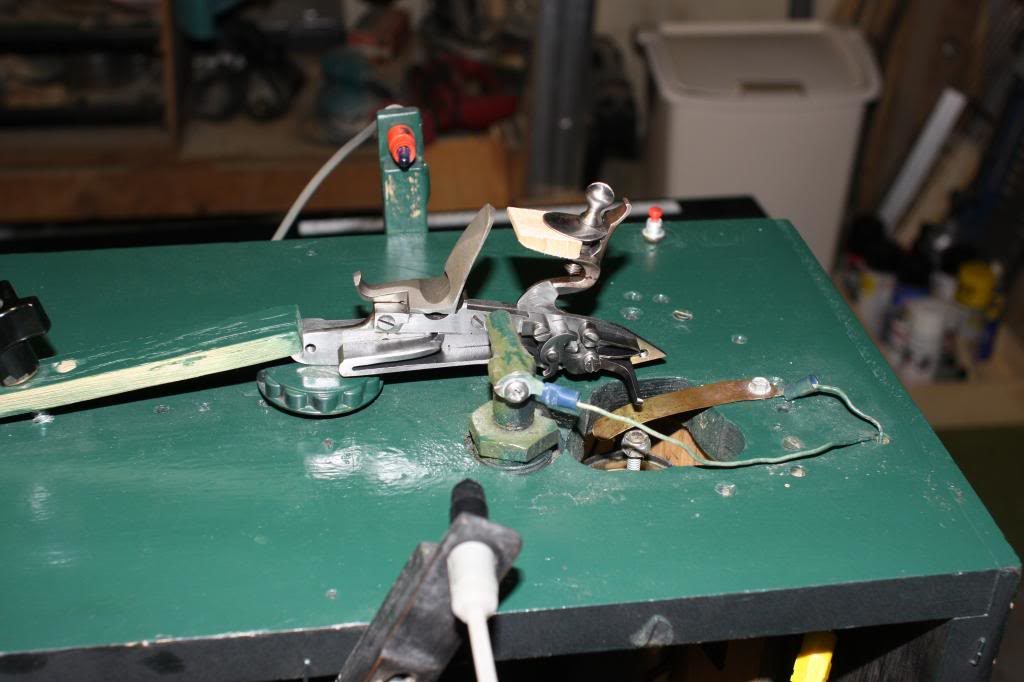
This shows the fixture from the back. Now the detector is in the forground. Here you can see the plunger below the sear with a thin brass blade between. When the plunger pushes the brass against the sear, the contact is made that starts time.
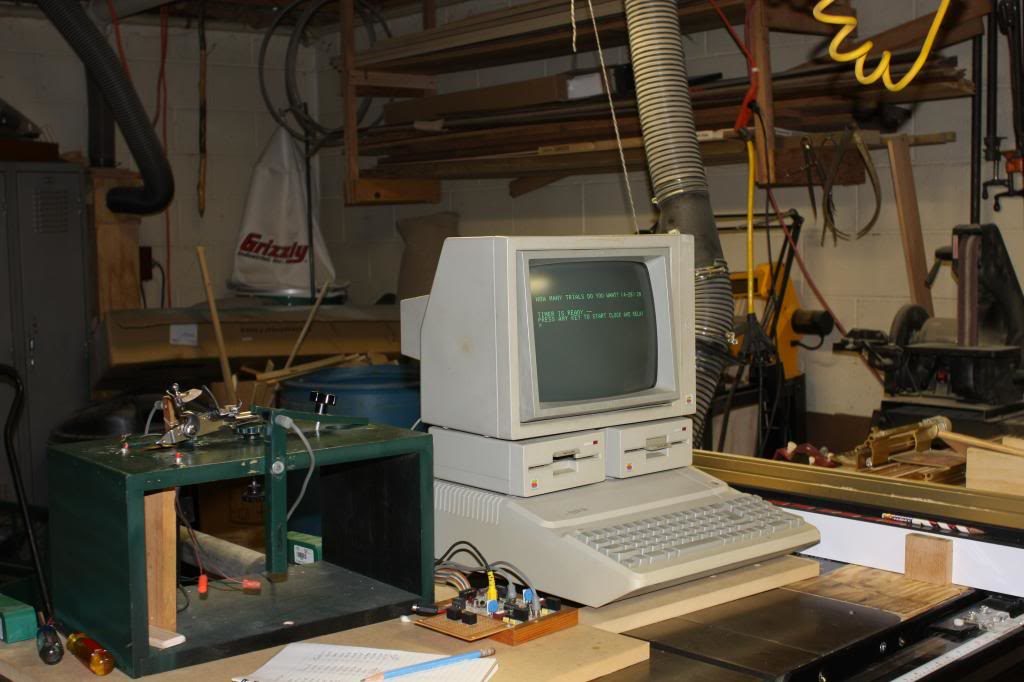
This last pic is the interface. The glowing green led lets me know that the infrared beam is not broken.
The mention of ultrasonic cleaning sounds interesting. Using brake parts cleaner sounds good too. Would the parts cleaner leave a coating that could be removed by alcohol? BTW, I figured alcohol would leave no coating. Hope that’s right. I should mention that I would use compressed air on the lock until no alcohol was left. I was surprised to see alcohol coming out of the sear and sear spring screws on the front of the lock plate.
The overlap is one reason these are IMHO statistically insignificant. As far as lube not removed, I think I got that solved after the first cleaning. After that I used plenty of alcohol and used compressed air until no alcohol came out – even from screw threads.
The real surprise was the substantial reduction in range shown by the Ballistol. While it had the slowest average, the lock was far more consistent with this lube. Methodology was the same throughout, so I have no explanation for Ballistol’s consistency.
I need to think about what material is the last step in the rinse before re-lubing. Is there a better fluid than alcohol? Other than ether (starter fluid) does anything leave NO residue? I feel that key to a clean lock means a final rinse with nothing left, including a residue of its own. Any ideas better than alcohol or ether?
The problem with a trace of oil in the compressed air was a possibility I hadn’t considered. As you probably read I moved my stuff from my garage into my basement when I didn’t need to use priming powder and flint. My garage air would have been filtered, but my basement compressor lacks a filter. I can rule out the problem by leaving the stuff in the basement but doing the lock cleaning in the garage. It adds a bit of time to the process, but lock-cleaning takes more time than running the tests anyway.
If I had a real lab behind me, some of those methods would probably be the answer. Since I’m a retired teacher working from my basement, I may have to settle on the best solvents readily available. I used alcohol as you know, but also have acetone and ether (starter fluid). One of my friends may have a couple more. I’ll give this more thought over the weekend and pick the brains of a couple local engineer friends.
In looking over the stats I am beginning to doubt what I know so far. Numbers within a trial vary so widely, I am beginning to look for an unknown variable. The problem is that solvents and methodology used so far have been the same throughout the tests. Is there a variable that widens the data that we haven’t anticipated. Just thinking. . .
Today I ran tests on more lubes plus another run of no lube. I have more photos to add but photobucket freezes every time I try to add another photo. The chart below contains both day’s work with day 2 at the bottom. I decided to leave in all the no lube groups when I saw that today’s was in about the same time category. I also highlighted the fast and slow time in each group. In a couple of cases the fast time and the slow time were next to each other in sequence. The ranking now includes all the trials from both days.
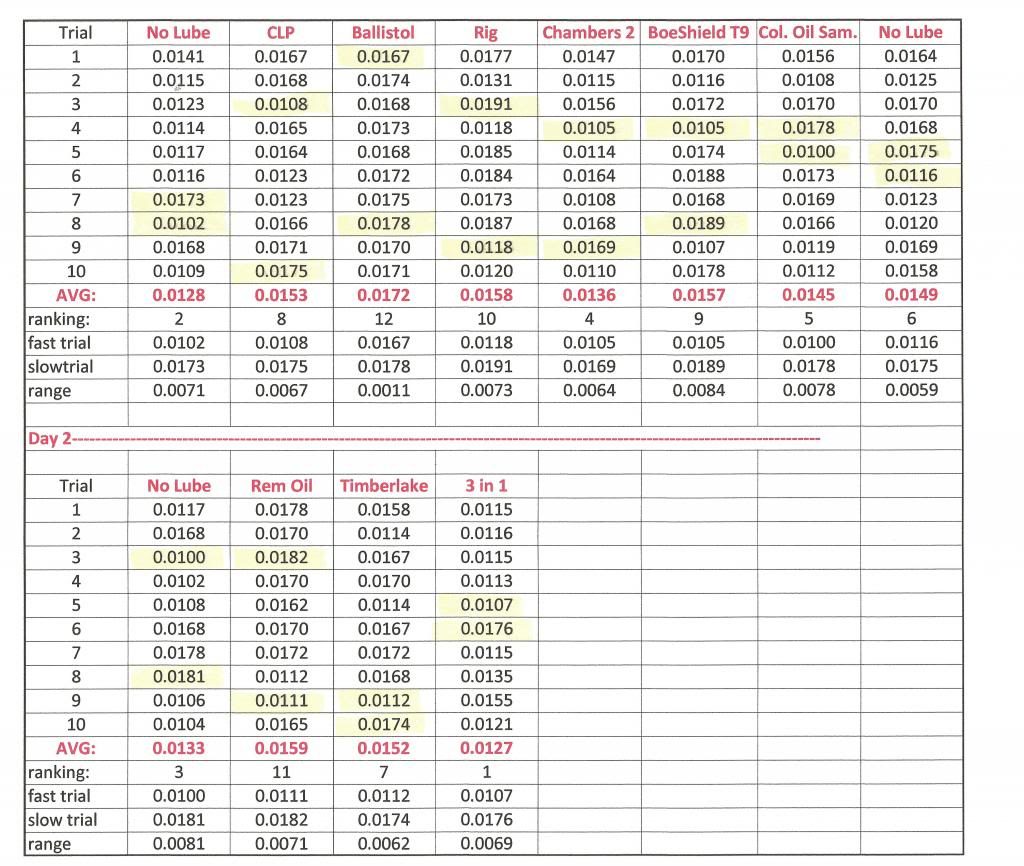
I changed cleaning methodology today. First I’m using filtered conpressed air to rule out the possibility of trace amounts of oil when drying the lock. Also, after using warm soapy water and a tooth brush on the lock, I used a series of 4 baths in acetone. I chose acetone over MEK because it evaporates more quickly. The purpose of the 4 baths was explained in an earlier post so I won’t go into that again. But I have confidence that trace amounts of oil are not involved in the testing.
After 2 days of timing, I feel that we will not find a super lube that is head and shoulders above the rest. Since the lock seemed faster with no lube, perhaps the trick is how to apply a very small amount. The containers that the oil comes in may play a part in this.
The wide range of times, especially overlapping as they do, make me conclude that lube quality does not influence the mechanical time of the lock. The question then is why not. My gut says that the very small amount of rotation is prehaps too brief to accurate measure the effect of lube. If we were dealing with a machine that rotated a number of revolutions, maybe we could see the difference. I don’t know.
If we do not choose a lube for speed, my choice would be to choose a lube for it’s ability to increase the life of the lock. I asked this question to Jim at Friendship. His answer was that he would choose a lube with the longevity of the lock in mind. My gut says we should too.
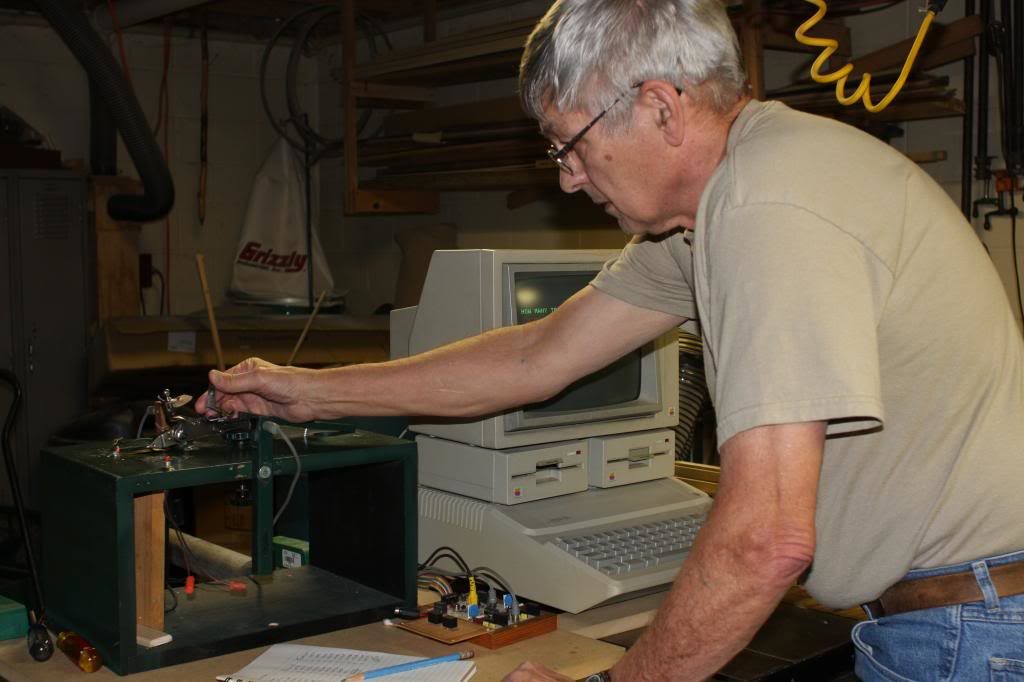